Understanding Error Sources in Precision Positioning
Errors in positioning devices can be broken down into two types: inaccuracy (predictable errors) and imprecision (random errors). Understanding the sources and magnitudes of these errors can help in formulating strategies for prevention and correction of them, and can result in higher confidence in the performance of your system. Below are details on some of the most important specifications used to describe the error in positioning devices, such as Zaber™ translation stages.
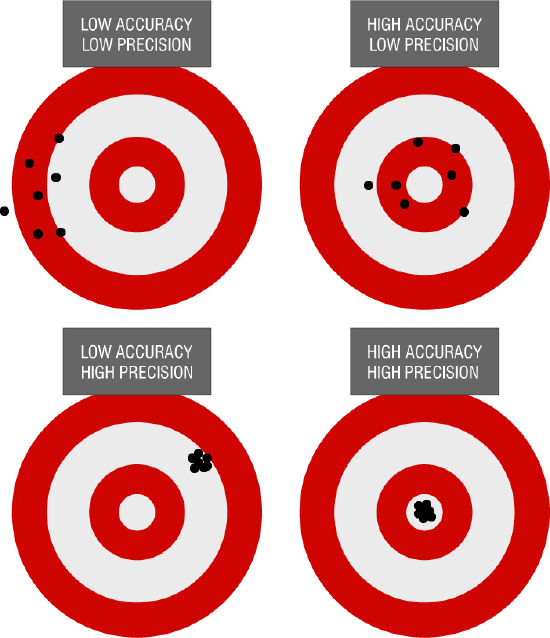
Figure 1: Illustrating the Difference Between Accuracy and Precision
Resolution
Resolution is a measure of the smallest distance change that can be requested. While it is an important feature for positioning applications, it is not a measure of accuracy or precision because it is a calculated value. It is based on specifications from the controller, motor, and mechanics, and because Zaber™ devices use stepper motors with microstepping drives, it can also be called the microstep size. While it is not a measurement of the error by itself, fine resolution is necessary to achieve accurate and precise movement.
Accuracy
When moving between any two points in the travel range, the accuracy specification indicates the largest deviation between ideal and actual distances travelled that can be expected. There are several error sources that account for this and over short travel distances, much less inaccuracy can be expected.
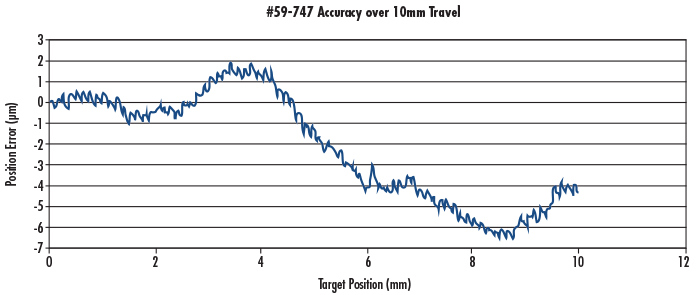
Figure 2: Accuracy of a the 150mm Zaber™ Linear Stage
Repeatability
Repeatability is the best measure of precision and consistency for a positioning device, and it is defined by the deviation in a position if it is approached multiple times from the same direction. For Zaber™ devices, it is typically at least an order of magnitude finer than the accuracy specification.
Backlash
Moving mechanical systems can have small gaps (or clearances) in the direction of motion in order to avoid being over-constrained. When changing directions, these clearances create a small amount of lost motion (or slack) that needs to be taken up. This is known as the backlash in the system.
For many systems, it is easy to account for this source of inaccuracy. One method is to be consistent in the direction that critical positions are approached from. Another is to apply a small axial force, which pushes the stage to one side of the gap. In vertical applications, gravity will apply the force that compensates for backlash.
or view regional numbers
QUOTE TOOL
enter stock numbers to begin
Copyright 2023, Edmund Optics India Private Limited, #267, Greystone Building, Second Floor, 6th Cross Rd, Binnamangala, Stage 1, Indiranagar, Bengaluru, Karnataka, India 560038
California Consumer Privacy Acts (CCPA): Do Not Sell or Share My Personal Information
California Transparency in Supply Chains Act