Highly Reflective Coatings
This is Section 11.4 of the Laser Optics Resource Guide.
Highly reflective (HR) coatings are used to minimize loss while reflecting lasers and other light sources. Absorption and scatter during reflection lead to decreased throughput and potential laser-induced damage. HR coatings are used in common laser optics applications such as folding a laser’s beam path and laser cavity end mirrors.
Metallic mirror coatings are used to create reflective components for many applications but laser applications tend to require a higher reflectivity than those offered from standard metallic mirror coatings. Because of this, multilayer dielectric HR coatings are usually used for laser mirrors instead of metallic mirror coatings, as they can achieve higher reflectivity. Metallic surfaces reflect light because loosely attached electrons freely oscillate with incident light waves without much impedance or hindrance, but all metals will absorb some amount of incident light. This makes metallic mirror coatings susceptible to damage when used with high power lasers.1
Dielectric HR coatings reflect light based on constructive interference during Fresnel reflections and have the complete opposite purpose of AR coatings in that they utilize constructive interference to maximize Fresnel reflections instead of utilizing destructive interference to minimize them (Figure 1). The constructive interference is caused by alternating layers of high and low refractive index materials with thicknesses specifically chosen to maximize reflectivity at a given wavelength range. In a λ/4 dielectric mirror, also known as a Bragg mirror, the thickness of each layer corresponds to a quarter of the design wavelength. Layer thickness is based on the wavelength in the material, not the vacuum wavelength.2
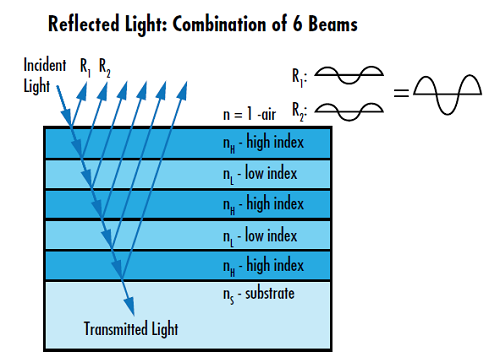
Figure 1: Dielectric HR coatings utilize constructive interference of Fresnel reflections to achieve a reflectivity greater than that of metallic reflectors
Dielectric overcoats also improve handling of metallic mirrors, increase the durability of the metal coating, provide protection from oxidation, and enhance the reflectance of the metal coating in specific spectral regions. Metal coatings are very delicate without a protective coating and require extra care during handling and cleaning. The surface of an unprotected metal coating should never be touched or cleaned with anything other than clean, dry air. Isopropyl alcohol or acetone can be used to clean metal mirrors with a dielectric coating. Table 1 shows a list of Edmund Optics’ standard metallic mirror coating options, while Table 2 shows a list of Edmund Optics’ standard dielectric HR laser coatings.
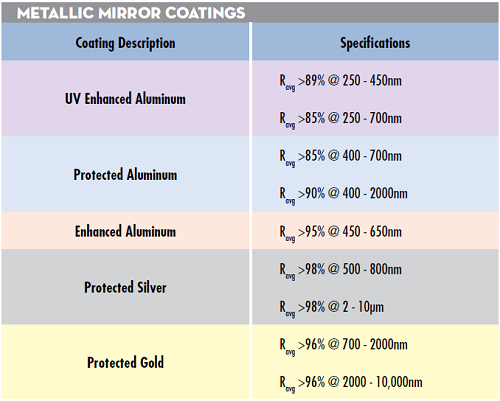
Table 1: Reflectivity specifications for Edmund Optics’ standard metallic mirror coatings
Table 2: Standard HR Laser Coatings | |||
---|---|---|---|
DWL | Reflectivity Specifications | LIDT, Pulsed $ \left( \frac{\text{J}}{\text{cm}^2} \right)$ |
LIDT, CW $ \left( \frac{\text{MW}}{\text{cm}^2} \right) $ |
266nm | Rabs >99.5% @ DWL, Ravg >99.5% 263 - 268nm | 2.5, 20ns @20Hz | 1 |
343nm | Rabs >99.8% @ DWL, Ravg >99.5% 339 - 346nm | 6, 20ns @20Hz | 1 |
355nm | Rabs >99.8% @ DWL, Ravg >99.5% 351 - 358nm | 6, 20ns @20Hz | 1 |
515nm | Rabs >99.8% @ DWL, Ravg >99.5% 509 - 520nm | 15, 20ns @20Hz | 1 |
532nm | Rabs >99.8% @ DWL, Ravg >99.5% 523 - 537nm | 15, 20ns @20Hz | 1 |
1030nm | Rabs >99.8% @ DWL, Ravg >99.5% 1020 - 1040nm | 20, 20ns, @20Hz | 1 |
1064nm | Rabs >99.8% @ DWL, Ravg >99.5% 1046 - 1074nm | 20, 20ns @20Hz | 1 |
Table 2: Reflectivity specifications and guaranteed laser-induced damage thresholds for Edmund Optics’ standard dielectric HR laser coatings. For other laser wavelengths, custom coating designs are available upon request
References
- Field, Ella S., et al. “Repair of a Mirror Coating on a Large Optic for High Laser-Damage Applications Using Ion Milling and over-Coating Methods.” Laser-Induced Damage in Optical Materials: 2014, July 2016, doi:10.1117/12.2067920.
- Paschotta, Rüdiger. Encyclopedia of Laser Physics and Technology, RP Photonics, October 2017, www.rp-photonics.com/encyclopedia.html
More Resources
- An Introduction to Optical Coatings
- Anti-Reflection (AR) Coatings
- Metallic Mirror Coatings Application Note
- Laser Optics Lab: Coatings Video
- Understanding and Specifying LIDT of Laser Components Application Note
- Modifying Stock Optics Tip #4: Add A Coating To A Stock Lens Video
- Benefits of Hard Coatings Application Note
- High Reflectivity Mirrors for Laser Applications Webinar
- Laser Optics Lab Video Series
or view regional numbers
QUOTE TOOL
enter stock numbers to begin
Copyright 2023, Edmund Optics India Private Limited, #267, Greystone Building, Second Floor, 6th Cross Rd, Binnamangala, Stage 1, Indiranagar, Bengaluru, Karnataka, India 560038
California Consumer Privacy Acts (CCPA): Do Not Sell or Share My Personal Information
California Transparency in Supply Chains Act