Diamond-Like Carbon and High-Durability AR Coatings
Authors: Victoria Marcune
Optical systems used in harsh environments face unique challenges in preventing component damage and system performance degradation. Diamond-like carbon (DLC) coatings and other highly-durable anti-reflective (AR) coatings are ideal solutions for these systems. DLC coatings feature a high hardness, low-friction surface with resistance to scratches and corrosion while providing excellent transmission in the mid- to long-wave infrared (IR). Their superior resistance and strength make them suitable for harsh, rugged environments and are ideal for thermal imaging and other defense applications. But they may not be the ideal choice for every situation, and understanding your other options for high-durability coatings lets you find the optimal solution for your given application. Edmund Optics® is skilled in designing and depositing DLC and other high-durability AR coatings.
What Are DLC Coatings?
DLC coatings take advantage of carbon’s tetravalent structure which allows for a variety of configurations to produce different physical properties. When found in a crystalline structure, carbon forms the well-known substance of diamond. This form is known to have the greatest hardness of any naturally-occurring substance on earth. Carbon arranged in a stable, hexagonal structure is known as graphite, which is capable of providing a low-friction surface. DLC coatings arrange the atoms into an amorphous structure which benefits from the desirable properties of both graphite and diamond.
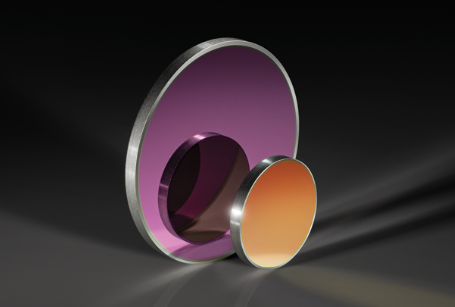
Figure 1: DLC coatings are a specialized type of AR coating well-suited for harsh environment applications because of their high hardness and resistance to scratches and corrosion.
DLC coatings start as a carbon-based gas which is plasma-assisted to form a uniform single layer coating across the substrate surface. This technique allows for the coatings to be applied to both flat and curved surfaces. Direct application to the surface is possible for substrates such as germanium and silicon, but some other substrates may require additional adhesion layers.
Highly-Durable AR Coatings
However, sometimes abrasion resistance and environmental protection are needed for visible or NIR wavelengths, or achieving high transmission becomes worth sacrificing a little bit of environmental protection. In these cases, non-DLC (but still highly durable) thin-film coatings may be the best option. Low reflectivities can be achieved while still achieving high levels of abrasion and environmental resistance. One example of a highly-durable AR coating is found on our High Durability Anti-Reflection (AR) Coated Sapphire Windows, which are ideal for harsh environments requiring thin optics.
DLC Coatings vs. Conventional AR Coatings
When compared to high-durability AR (HDAR) and standard AR coatings, DLC coatings are the most tailored for hardness and durability. Abrasion testing to military durability standards MIL-C-48497, MIL F-48616, and MIL-C-675 is done by rubbing the part with a standard rubber pumice eraser conforming to MIL-E-12397 with a bearing force between 2 – 2.5 lbs. applied normal to the coated surface. The part is tested for 20 – 200 strokes, depending on the end application. DLC coatings also undergo wiper testing to TS-1888 guidelines. Corrosion testing is also performed, including salt fog testing, salt water spray testing, and accelerated corrosion testing to help predict in-field performance of the optic. Edmund Optics® DLC coatings are found to be salt fog testing compliant for 90+ days.
DLC coatings exhibit great broadband transmission over IR wavelengths, but on average have slightly less throughput compared to standard BBAR coatings (Figure 2). To mitigate light loss, DLC coatings are often paired with traditional AR coatings on the back surface of the optic. This will produce high transmission at a narrower bandwidth than optics with BBAR coatings on both surfaces while benefitting from the high durability of DLC coatings on one side of the optic. Fourier-transform infrared (FTIR) technology is often used to analyze DLC coating performance.
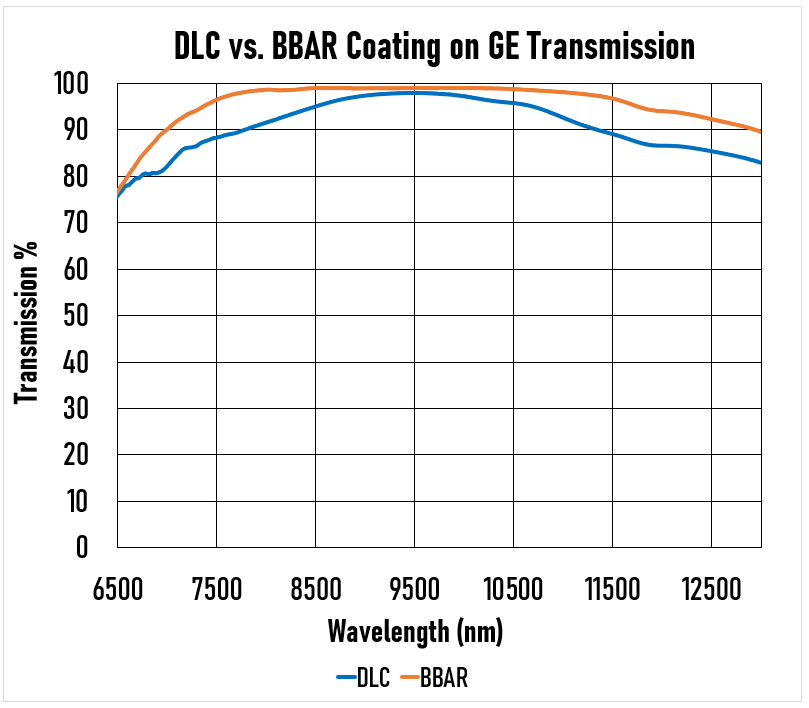
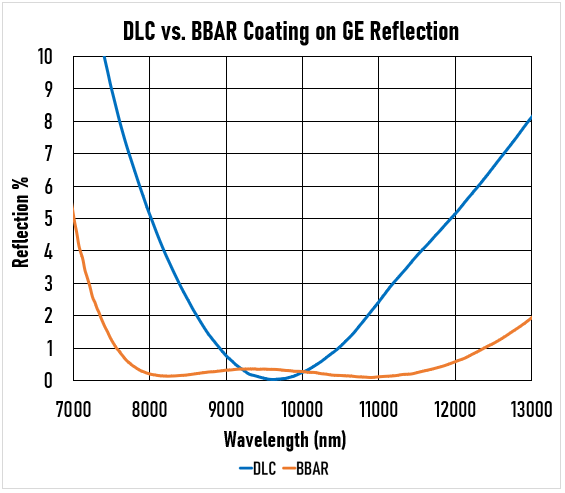
Figure 2: Transmission and Reflection curves for DLC and BBAR coatings on a germanium substrate. The DLC coating produces a V-shaped reflectivity curve and will typically have less transmission than the BBAR coating.
Advantages | Disadvantages | |
---|---|---|
DLC Coatings | Durability | Transmission |
Conventional BBAR in the mid-IR | Transmission | Durability |
Table 1: Comparison of DLC coatings to conventional BBAR coatings.
But again, sometimes other highly-durable AR coatings are preferred if operating at shorter wavelengths or if minimizing reflectivity is especially important. These non-DLC coatings can still be made to be abrasive resistant, meeting MIL-C-675 requirements. Figure 3 shows two sample reflectance plots from our High Durability Anti-Reflection (AR) Coated Sapphire Windows.
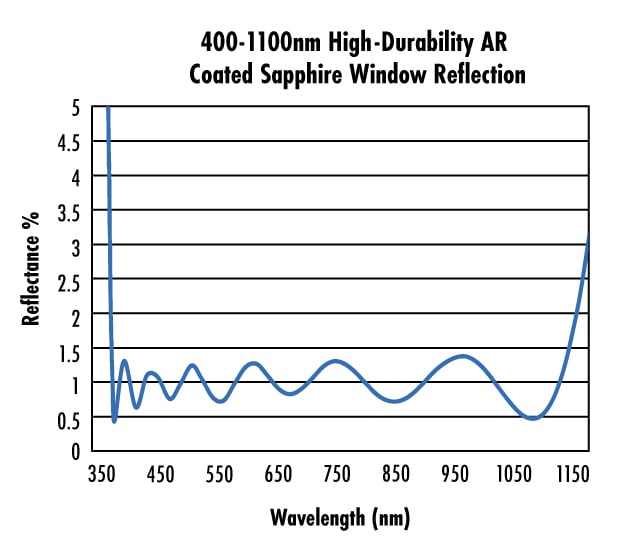
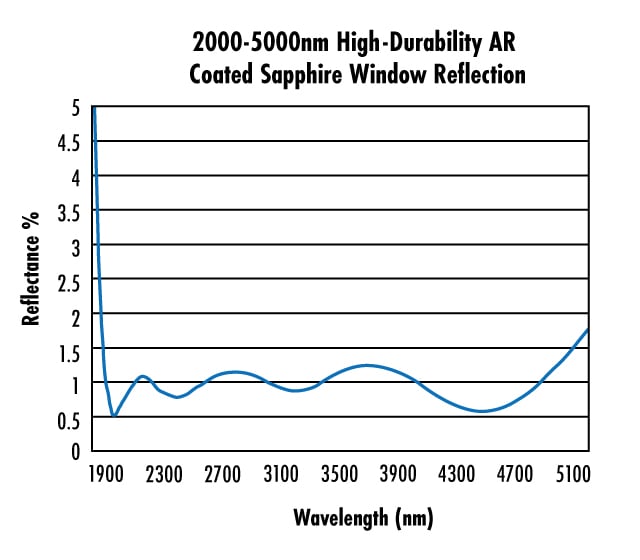
Figure 3: Reflection curves for sample thin-film highly-durable AR coatings. These are a balance between conventional AR and DLC coatings.
DLC Coatings at Edmund Optics®
Edmund Optics is at the forefront of DLC coating technology, providing both off-the-shelf DLC-Coated Germanium Windows and manufacturing custom DLC-coated optics. We deposit DLC coatings on both germanium and silicon substrates.
For custom DLC-coated optics, in-house grinding, polishing, and diamond turning are available. Coatings can be fine-tuned to provide maximum transmission at desired wavelengths. In-house environmental testing, wiper testbeds, and FTIR spectrometers ensure that all specifications are met.
Highly-Durable AR Coatings at Edmund Optics®
Edmund Optics also designs and deposits thin-film highly-durable AR coatings that can achieve the severe abrasion requirements of MIL-C-675C while achieving low reflectivities. Click below to learn more about the wide range of coating types that we can design for you.
References
- Peterson, N. (2022, January 16). What is DLC, Also Known as Diamond Like Carbon Coating? https://vaportech.com/blog-what-is-diamond-like-carbon-dlc/
or view regional numbers
QUOTE TOOL
enter stock numbers to begin
Copyright 2023, Edmund Optics India Private Limited, #267, Greystone Building, Second Floor, 6th Cross Rd, Binnamangala, Stage 1, Indiranagar, Bengaluru, Karnataka, India 560038
California Consumer Privacy Acts (CCPA): Do Not Sell or Share My Personal Information
California Transparency in Supply Chains Act